Three Types of Safety Audit every GMR 2.1 and GCC Factories Candidate must know
- Nkululeko Thusini
- Feb 4
- 7 min read
When I started working in safety compliance, I quickly learned that understanding and implementing the right safety audit was not just a matter of ticking boxes—it was about protecting people, resources, and our organization's reputation.
Over the years, I've come to appreciate that each audit type serves a unique purpose, and knowing when and how to deploy them can make all the difference.
Today, I'd like to share my experience with three fundamental types of safety audits that every legal appointee needs to be conversant with.
Legal appointees working under frameworks like General Machinery Regulation (GMR) 2.1, Mine Health and Safety Regulation (MHSR) 2.13.1, Construction Regulation (CR 8.1, Explosives Regulation (ER) 12.1, and similar regulations must master the following:
Compliance-based safety audits
Risk-based safety audits
Behavior-based safety audits
Diving into Compliance-Based Audits that can help GMR 2.1 and GCC Factories Candidates ensure safety compliance
When I first encountered compliance-based audits, I thought they were straightforward.
After all, they essentially involve checking if everything aligns with regulatory requirements and internal safety policies.
In many ways, that's precisely what compliance-based safety audits do.
The process involves using comprehensive checklists that capture every required standard detail. These audits are the backbone of any safety program because they ensure the organization meets all legal and internal mandates.

I remember my early days on the job, meticulously going through every checklist item with the precision of a detective. We had a well-documented set of procedures, and the goal was to verify that all these were in place and actively followed.
During one particular audit, I spent hours verifying that fire safety equipment complies with Pressure Equipment Regulation 19, SANS 543, and SANS 1128. It was a bit mundane, but it had to be done.
The repetitiveness of the task underscored its importance: without compliance, the entire safety framework could crumble under legal scrutiny or, worse, during an emergency.
However, the most valuable lesson I learned from compliance-based audits was the importance of documentation. Every checklist item guided us in what we had to accomplish and demonstrated that the organization was serious about safety.
The checklists that you compile depend a lot on the regulations the organization has to comply with. In our case, we had the following checklists:
Overhead crane yearly inspection tracking sheet to ensure compliance with Driven Machinery Regulation 18.
Pressure equipment 36-monthly inspection tracking sheet to ensure compliance with Pressure Equipment Regulation 11.
Lift two yearly inspection tracking sheets to ensure compliance with Lift, Escalator, and Passenger Conveyor Regulation 6.

The first step to developing the compliance tracking sheets is determining which regulations your organizations need to comply with.
You can dive deep into those regulations to determine the specific requirements.
You will also notice that some regulations refer you to Health and Safety Standards, where you must further determine the other compliance items. For example, pressure equipment regulation 3 requires categorizing pressure equipment according to SANS 347.
In regulated industries, these audits protect the company from potential legal actions by demonstrating that the team took every possible step to mitigate hazards.
I felt a sense of accomplishment knowing that my detailed reports contributed to a culture of accountability and diligence.
The Proactive Nature of Risk-Based Audits that can help GMR 2.1 and GCC Factories Candidates ensure safety compliance
While compliance-based audits are fundamental, they can sometimes feel reactive—they confirm that all the rules are being followed.
Risk-based audits address the shortcomings of compliance-based safety audits.
I quickly discovered that these audits are about more than just checking boxes; they identify and prioritize potential hazards before they lead to incidents.
Risk-based audits require a thorough risk assessment involving analyzing potential hazards' risk levels (likelihood x severity).
I recall the numerous steam generator modifications where we had to do Hazard and Operability (HAZOP) studies. Instead of confirming that existing safety protocols were adhered to, we dug deep into what could go wrong.

We analyzed historical data, ran simulations, and conducted scenario-based planning exercises to predict potential incidents.
The HAZOP study assisted in proactively identifying high-risk areas that hadn't been on our radar before.
What struck me most during that process was how dynamic and forward-thinking risk-based audits are. Risk-based audits require critical thinking and adaptability, unlike compliance audits, which rely heavily on predetermined checklists.
ISO 45001 emphasizes understanding the organization's context, and these guidelines assist in understanding the unique context of each operation. In one instance, after identifying a potential risk area, we implemented additional safety measures and training programs that significantly lowered the risk of an incident.
Safety isn't static—it's an ever-evolving challenge that requires continuous vigilance and innovation.
Risk-based audits also highlight the importance of prioritization. By focusing on areas with the highest potential for incidents, we were able to allocate our resources more efficiently. This was particularly useful in large organizations where addressing every safety issue at once is impractical. By understanding the source of the most significant risks, we could implement targeted interventions, ultimately preventing incidents rather than reacting to them.
Cultivating a Culture with Behavior-Based Safety Audits that can help GMR 2.1 and GCC Factories Candidates ensure safety compliance
If compliance-based and risk-based audits ensure that safety's technical and procedural aspects are covered, behavior-based safety (BBS) audits address the human factor.
My journey with behavior-based safety audits was both eye-opening and transformative. They revealed how our actions, attitudes, and habits contribute to safety.
I was fortunate to work for a leading petrochemical company that significantly emphasized BBS. There, I saw how effectively implementing BBS identified and prevented possible safety incidents.
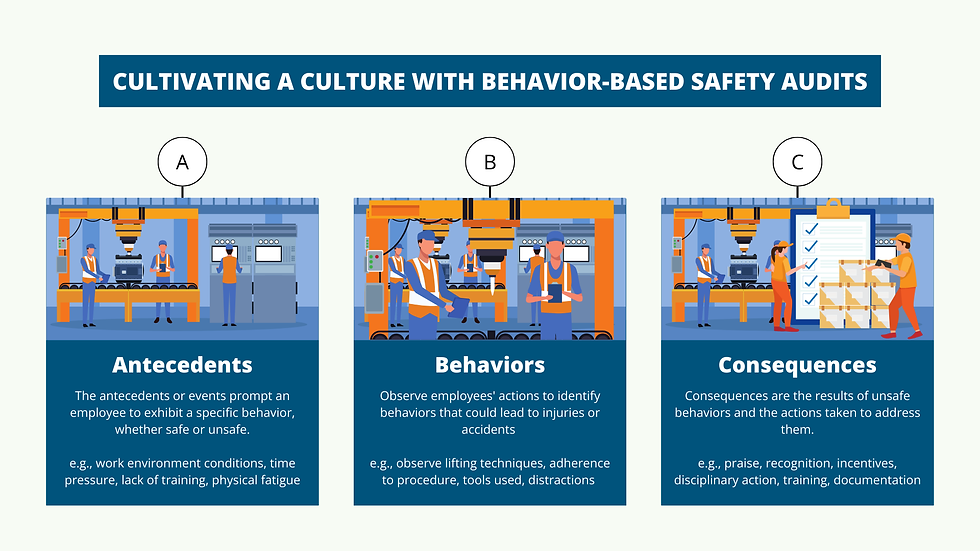
BBS audits focus on observing and evaluating employee work practices.
They go beyond the physical aspects of safety to understand the behaviors that underpin safe or unsafe practices. I remember conducting an audit in a petrochemical environment, where I spent a day observing employees. Rather than using a rigid checklist, I engaged in conversations, asked questions, and carefully observed how employees performed tasks. This experience influenced my designs and compilation of maintenance and operations procedures.
It became clear that certain risky behaviors could undermine overall safety even when all equipment was up to standard.
One of the key strategies I employed was direct observation. By watching how employees performed tasks, I could identify patterns not immediately apparent through other audit types. For instance, under time pressure, I noticed that some employees bypass specific safety protocols to speed up their work.
While the equipment and environment were safe, these behaviors created potential hazards that could lead to accidents. Addressing these behaviors through coaching and targeted training sessions improved the safety culture.
Employee interviews also played a crucial role in behavior-based audits. These conversations often revealed underlying issues such as lack of training, misunderstandings about safety procedures, or even personal attitudes towards risk.
I remember one interview where an employee candidly shared that specific safety protocols seemed overly cumbersome and impeded their workflow. This feedback was invaluable because it allowed us to reassess and streamline some procedures, making them more user-friendly without compromising safety.
By involving the workforce in the audit process, we fostered a sense of ownership and accountability among employees, essential for a robust safety culture.
Implementing behavior-based safety audits requires a shift in mindset.
It's about moving from a blame culture—where mistakes are punished—to a learning culture that reinforces safe behaviors and corrects unsafe practices through constructive feedback.
I found that this approach improved safety outcomes and boosted morale and engagement among the team. When employees see that their insights lead to real change, they become more invested in maintaining a safe working environment.
Bringing It All Together
In my years of experience, I've come to appreciate that each type of safety audit has distinct strengths. When used together, they provide a comprehensive framework for ensuring safety compliance.
Here's how they complement each other:
Compliance-based audits lay the groundwork for achieving all legal and policy-based requirements. They serve as a solid foundation for all other safety measures.
Risk-based audits take this foundation and add a layer of proactive analysis, identifying potential hazards before they turn into incidents. This approach helps prioritize efforts and resources where they are needed most.
Behavior-based safety audits focus on the human element, addressing the behaviors and practices that underpin safe operations. By engaging directly with employees, these audits foster a culture of continuous improvement and shared responsibility.
For any legal appointee working under regulatory frameworks like GMR 2.1, MHSR 2.13.1, CR 8.1, ER 12.1, and others, mastering these audits is not merely an obligation—it's an opportunity to drive meaningful change.
The unique focus and methodology of each audit type provide critical insights that help build a safer, more resilient organization.
Lessons Learned and Future Perspectives
Reflecting on my journey, I've learned that safety audits are not just about compliance, risk management, or behavior modification in isolation—they're about creating an integrated safety culture.
This culture emphasizes that safety is everyone's responsibility.
Whether through meticulous documentation, proactive risk analysis, or engaging with employees on the shop floor, every step taken is a step toward a safer environment.
Looking ahead, I'm excited about the potential of combining traditional audit techniques with modern technology. Digital checklists, real-time data analytics, and even AI-powered predictive tools are beginning to revolutionize safety audits.
Imagine a scenario in which machine learning algorithms enhance risk-based audits by predicting potential hazards based on historical data or where behavior-based audits leverage wearable technology to monitor real-time safe practices.
The future of safety audits is dynamic and filled with promise.
As I continue to navigate the complexities of safety management, I remain committed to the belief that thorough, well-implemented audits are not just regulatory obligations—they are vital investments in our most valuable asset: our people.
I encourage all legal appointees and safety professionals to embrace the multifaceted approach of combining compliance-based, risk-based, and behavior-based audits. In doing so, we meet the requirements of our roles and pave the way for a safer, more proactive, and inclusive work environment.
My journey with safety audits has taught me that while the tools and techniques may evolve, the core principle remains: safety is a continuous journey, not a destination.
Every audit, observation, and feedback session contributes to a larger narrative of care, diligence, and excellence. I invite you to join me on this journey, learn from each audit, and champion a culture of safety wherever you go.
Next Steps
Fostering a safety culture does not happen overnight and requires constant training and employee awareness campaigns.
That is why Palucraft developed the 'Understanding and Fulfilling the Role of the GMR 2.1' short course, which provides the insights, tools, and resources to be a successful and competent legal appointee such as the GMR 2.1 required in terms of the General Machinery Regulations.
It may be worthwhile considering completing the short course, which takes a deep dive into developing safety audit templates that you can use at your organization.
Click here to learn more about the short course.
コメント